硅砖生产工艺介绍
发布时间:2022/6/9 11:14:02 点击率: 来源:高铝砖厂家 作者:荣盛耐材 硅砖的价格居高不下,因为是成品率低,某一环节出现问题就会受到影响,下面介绍一下硅砖的生产工艺,请看详细内容。
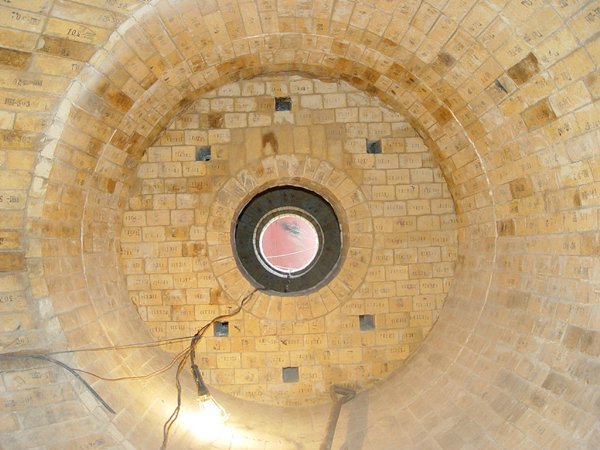
硅砖生产的工艺流程大体上与粘土砖的工艺流程相似。不同点在于前者增加了石灰和矿化剂的制备系统。
一、颗粒组成的选择
硅质坯体加热时的松散和烧结能力取决于颗粒组成中粗细两种粒度的性质和数量。
采用细颗粒组成的砖坯时,在烧成时有利于减少膨胀,减少砖体的裂纹和体积变化,提高成品率,还可提高制品中鳞石英的含量,但泥料颗粒过细,也将导致硅砖气孔率的提高。
一般硅砖的临界粒度以2~3mm为宜。
制造硅砖选用的结合剂
制造硅砖用的结合剂有亚硫酸纸浆废液和石灰乳。用石灰乳作结合剂时,它起着塑化剂的作用。石灰乳使砖坯在干燥过程中增加强度,在烧成时则成为矿化剂,促进石英的转化。
石灰应含有大量活性CaO,未分解的CaCO3和MgCO3不超过5%,Al2O3+Fe2O3+SO2F超过5%。当含有大颗粒欠烧Ca-CO3和过烧石灰时,制品产生熔洞,影响制品质量。
配料时应将石灰的加入量换算成CaO,其加入量视制品的不同而异,通常波动在1.5?2.5%。例如,生产焦炉硅砖,CaO加入量为2.0?3.0%;生产电炉顶硅砖,CaO加入量为1.4?1.75%。
硅砖的配料特点
采用杂质含量小于0.5%的优质硅石,配料前用自来水冲洗,以保证前期质量。配料时将快转化石英与慢转化石英混合配料,可使烧成温度降低20℃。配料过程中将临界粒度由3mm降至2mm,可增加物料的界面能,促进石英的转化。
此外,选用新型矿化剂,对提高产品质量也很重要。目前,大多数生产者在配料中加入的矿化剂仍是石灰乳和铁鳞。为提高制品的荷重软化温度,FeO的加入量已从2.5%降至1%以下。如果采用长石类含有碱金属的矿物或复合矿化剂都可以收到较好的效果。
制备硅砖泥料的加料顺序
将各种硅石粉和废硅砖粉按一定配比加入湿碾机中,先干混2?3min,再加入亚硫酸纸浆废液、石灰乳及氧化铁粉的混合液,根据成型方法的要求,再混合8?17min。
泥料混合时间的长短取决于碾轮重量、碾盘转数,原料加入量、原料硬度、泥料的颗粒组成及成型方法。特异型砖和手工成型用的泥料比机械成型用的泥料要求有较长的混合时间。对于不同泥料的混合时间,应由实验来确定。
制造硅砖用泥料的水分一般为5?9%,手工成型泥料水分为7?9%,机械成型用泥料水分为5?6%。
二、成型:
硅砖成型的特点表现在硅砖坯料成型特性和硅砖砖型形状复杂与质量差别大等方面。硅质坯料是质硬、结合性和可塑性低的瘠性料,因此它受压而致密的能力低。硅质坯料的成型性能受其颗粒组成、水分和加入物的影响。调整这些因素可以改善坯料的成型性能。对任何组成的坯料,增加成型压力都会提高硅砖密度。为了保证制得致密砖坯,成型压力应不低于100~150MPa。
三、烧成
硅砖在烧成过程中发生相变,并有较大的体积变化,加上砖坯在烧成温度下形成的熔液量较少(约10%左右),使其烧成较其它耐火材料困难得多。硅砖的烧成制度与砖坯在烧成过程中所发生的一系列物理化学变化,加入物的数量和性质,坯体的形状大小以及烧成窑的特性等因素有关。
1、硅砖在烧成过程中的物理化学变化在150℃以下从砖坯中排出残余水分在450℃时,Ca(OH)2开始分解;450~500℃时Ca(OH)2脱水完毕,硅石颗粒与石灰的结合破坏,坯体强度大为降低。在550~650℃范围内,b—石英转变为α—石英,由于转变过程中伴有0.82%的体积膨胀,故石英晶体将出现密度不等的显微裂纹。
在600~700℃间,CaO与SiO2的固相反应开始,砖坯强度有所增加,反应式为:
2CaO+Si02→b一2CaO·SiO2
2CaO·Si02+Si02→2(CaO·Si02)
至1000~1100℃有固熔体状α-CaO·Si02与FeO·SiO2生成。
α-CaO·SiO2+FeO·SiO2→[GaO·SiO2—FeO·SiO2]
从l100℃开始,石英的转变速度大大增加,砖坯的密度也显著下降,此时砖坯体积由于石英转变为低密度变体而大为增加。虽然此时液相量也在不断增加,但在1100~1200℃范围内仍易产生裂纹。
在1300~1350℃时,由于鳞石英和方石英数量增加,砖坯的密度降低得很多。此时液相粘度仍较大,对内应力的抵抗性还弱,生成裂纹的可能性存在。当加热到1350~1430℃时,石英的转变程度和由此产生的砖体膨胀大大增强,在这一温度范围内,加热得愈缓慢,石英溶于液相再结晶生成的鳞石英量愈多,方石英生成量愈少,砖体生成裂纹的可能性也愈小。如果加热过快,特别是在氧化气氛下迅速加热,石英转变为方石英,使砖坯松散并出现裂纹。
2、烧成制度
在600℃以下,可用较快而均匀地升温速度烧成。 在700℃以上至1100~1200℃温度范围内,因砖坯体积变化不大,强度逐渐提高,不会产生过大应力,只要保证砖坯加热均匀,可尽快升温。
1100~1200℃至烧成终了温度的高温阶段,硅砖的密度显著降低,晶体转变及体积变化集中地发生在这一阶段。它是决定砖坯出现裂纹与否的关键阶段。这个阶段升温速度应逐渐降低,并能缓慢均匀升温。
为了在高温阶段使温度缓慢均匀上升,在生产中通常采用弱还原火焰烧成。同时还可以使窑内温度分布均匀,减少窑内上下温差,避免高温火焰冲击砖坯,达到“软火” (均匀缓和火烧成)烧成要求。
硅砖高烧成温度不应超过1430℃。
硅砖烧成至高烧成温度后,通常根据制品的形状大小,窑的特性,硅石转变难易,制品要求的密度等因素,给以足够的保温时间。硅砖烧成后的冷却,高温下(600~800℃以上)可以快冷,低温时因有方石英和鳞石英的快速晶型转变,产生体积收缩,故应缓慢冷却。
在制定烧成曲线时,除应符合上述要求外,还应考虑:
1)原料的加热性质;
2)加入物的数量和性质;
3)砖块的形状大小。其他如烧成窑的结构、大小、装窑方法、窑内温度分布等均有影响。
烧成升温速度一般可划分为如下几个阶段;
温度范围,℃ 升温速度℃/h
20~600 20
600~1100 25
1130~1300 10
1300~1350 5
1350~1430 2
- 上一篇:耐火砖的比热容是多少?
- 下一篇:有耐2000度高温的耐火材料吗?